What is an Example of Flexo Printing?
Introduction: Flexography, also known as flexo printing, is a popular method of printing on flexible materials such as plastic films, packaging materials, and textiles. It has gained widespread popularity due to its ability to produce high-quality prints at a faster rate and lower cost compared to other printing methods. In this blog post, we will explore an example of flexo printing to understand its process and applications.
FLEXO PRINTING MACHINE
10/28/20232 min read
Introduction:
Flexography, also known as flexo printing, is a popular method of printing on flexible materials such as plastic films, packaging materials, and textiles. It has gained widespread popularity due to its ability to produce high-quality prints at a faster rate and lower cost compared to other printing methods. In this blog post, we will explore an example of flexo printing to understand its process and applications.
Understanding Flexography:
Flexography is a relief printing technique that uses a flexible rubber plate with raised images or areas called "flexograms." These flexograms are inked and then transferred onto the substrate, resulting in a printed image. The flexibility of the rubber plate allows it to conform to the contours of the substrate, making it ideal for printing on irregular surfaces.
Example of Flexo Printing:
One common example of flexo printing is the production of food packaging labels. Let's take a closer look at how flexography is used in this application.
1. Preparation of the Flexographic Plate:
The first step in flexo printing food packaging labels is the preparation of the flexographic plate. A skilled graphic designer creates digital artwork that represents the desired label design. This artwork is then converted into a negative image, which is used to create a raised flexogram on a flexible rubber plate using photolithography techniques.
2. Inking and Application:
Once the flexographic plate is prepared, it is time for inking and application. The flexographic plate is mounted on a rotating cylinder, and ink is applied to the raised areas of the flexogram. The ink is typically water-based or solvent-based, depending on the specific requirements of the printing process.
3. Printing Process:
The printing process involves transferring the inked flexogram onto the substrate, which in this case is a sheet of paper or film used for food packaging labels. The substrate moves past the rotating cylinder, and the ink is transferred from the flexogram onto the substrate through a combination of pressure and heat. This results in a high-quality printed label with vibrant colors and sharp details.
4. Varnish Application (optional):
After the printing process, a varnish layer may be applied to enhance the durability and protection of the printed label. This varnish can provide additional gloss, UV resistance, or other desired properties depending on the specific requirements of the label application.
Conclusion:
Flexography, or flexo printing, offers numerous advantages over other printing methods, particularly when it comes to printing on flexible materials like food packaging labels. Its ability to produce high-quality prints quickly and efficiently makes it an essential technology in the packaging industry. By understanding the process and examples of flexo printing, we can appreciate its significance in creating visually appealing and functional labels for various products.
If you found this article helpful and would like to inquire about our rotary flexographic printing machines or any of our related products and services, please feel free to fill out the form below. Our team will be happy to assist you with any questions or concerns you may have. We look forward to hearing from you!
REQUEST A QUOTE
Send us a message if you have any questions or request a quote. We will be back to you ASAP!
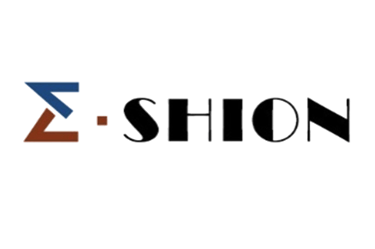
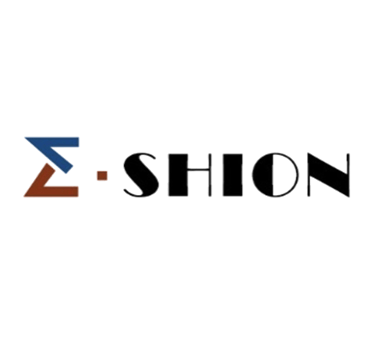
Copyright @ 2025
Address:Zhixin Industrial Zone, Ruian City, Wenzhou, Zhejiang Province, China
Phone: +8615167789726
Tel / Fax : +86-577-66811321
Email:doris@e-shionmachine.com
E-SHION Machinery is a professional plastic machinery manufacturer, providing high-quality film blowing machines, bag making machines and printing machines, providing one-stop plastic processing solutions for global customers.